Control
electronics for AlfaSpid BIG-RAS rotator with graphical display
The controller is primarily designed for
BIGRAS rotators, but it can
also be used for other rotators that use pulse feedback. By turning off
the vertical rotation, full use of RAK or BIGRAK rotators is also
possible. In the case of
a small modification of the firmware, it can also be used with analog
feedback (YAESU). Three sizes of displays can be used for the
controller. 1.9" like in the picture, as well as
2.4" and
2.8". It is important the display needs to have an ST7789 type chip.
Available
functions:
The controller can be controlled in four ways. One
of the two
USB
ports on the board is a native USB 1.1 type, with a speed of 12 Mbps.
The other USB port is a USB-UART converter, its transmission speed is
fixed at 115200 Bd. In addition, a standard RS232 COM port can be used
via a TTL-RS232 converter. Its speed can be set between 300 and
230400
Bd. With the right program, it is also possible to control via WiFi.
The mentioned options can even be used at once.
The settings are also
available either directly from the
controller, via a serial port, or via WiFi, in which case we can change
the settings by opening the appropriate web page. The main commands of
the controller are compatible with the Yaesu GS232, so it should be
selected if necessary. The full command set is available through the
serial port with the H command. In addition to Yaesu commands, it can
interpret FOXDELTA type commands as well as standard NMEA type GPGGA
messages. If we have previously set our own coordinates, it calculates
the azimuth and elevation of the given point based on the data in the
messages, and then turns the antenna in the direction of the given
point. This function is mainly used for tracking high-altitude balloons
(for example, the program called SondeMonitor has such an output, so
this program can rotate the antenna straight).
The controller can also emulate the PSTRotator and rotctld programs. So
if in one of the programs we use the control of the rotor is only
possible with the PSTRotator or rotctl protocol (e.g. SatDump, Horus),
we just need to set the appropriate port number in both places, and in
the program we use the controller's IP address, which we see in the
upper left corner of the Menu window. Of course, it is necessary to be
connected to the WiFi network.
Description:
The central element of the control circuit is an
ESP32-S3 N16R8
type module. We need to get the module shown in the picture, because
there is
also a version on the market where the push buttons are directly above
the USB connectors. However, this module is 2.54 mm narrower, so it
will not fit into the PCB due to the pins location. Some manufacturers
sell the module with a
loaded demo program, which flashes the LED on the module after
switching on. If you managed to get one like this, you have to
dismantle the
short circuit marked RGB on the module. Next to the RGB LED is another
short cut labeled IN-OUT. This has to be cut short! A uPython
interpreter
runs in the module, which interprets and
executes the code written in Python.
In order to simplify the preparation, a ready-made module of type IBT_2
was
used for controlling the motor itself. The
display and push buttons are located on a separate small panel. Since
the COM connections are already obsolete, it would not have been
reasonable to integrate it on the PCB, but if necessary,
this module can also be connected separately. There are 5 push buttons
on the display panel. Their function depends on the current situation.
The function of which button is indicated in the bottom line of the
display. If both horizontal and vertical rotation are active, then from
left to right: antenna down, antenna up, stop or menu, antenna to the
left (counter-clockwise), antenna to the right (clockwise). If only
horizontal rotation is active, the far left button is left turn, the
right far button is right turn, the middle one is stop. The second and
fourth buttons have no function.
The use of the following functions is only for
convenience and does not affect the main functionalities of the
controller. Their installation is not absolutely necessary. The P1 and
P2 potentiometers can be used to turn the antenna to the desired
position more easily, by setting the desired direction with the
potentiometer, then pressing the SW7 button, the antenna moves
horizontally, while pressing the SW8 button, the antenna moves
vertically, to the selected position. We can use a common potentiometer
for the horizontal and vertical directions, or a separate potentiometer
for the horizontal and one for vertical directions. If the value of the
pot parameter in the rotor_s3.cfg file is 1, it assumes a common
potentiometer, if the value is 2, it means that there are two separate
potentiometers. Since this parameter is not changed during use, this
parameter can only be rewritten manually with a text editor in the
previously mentioned file. When the third push button (SW9) is pressed,
the antenna moves to the parking position set in the menu. So that the
potentiometers does not have to be calibrated, when SW10 is pressed,
the position set with the potentiometers is shown on the display. Thus,
when turning the potentiometers, we can see where the antenna will turn
when SW7 or SW8 is pressed.
The main commands that can be
used to rotate the antenna:
Waaa eee - turn the antenna horizontally to aaa, vertically to eee
A - stop azimuth turning
AZ=aaa - turn the antenna horizontally to aaa
AZ=aaa EL=eee - turn the antenna horizontally to aaa, vertically to eee
E - stop elevation turning
EL=eee - turn the antenna vertically to eee
S - stop all turning
Maaa - turn the antenna horizontally to aaa
Keee - turn the antenna vertically to eee
ML - turn the antenna counterclockwise
MR - turn the antenna clockwise
MU - turn the antenna up
MD - turn the antenna down
L - turn the antenna counterclockwise
R - turn the antenna clockwise
U - turn the antenna up
D - turn the antenna down
C - the current position of the antenna in the horizontal direction
C2 - the current position of the antenna in horizontal and vertical
directions
B - the current position of the antenna in the vertical direction
For the antenna calibration to work properly, a
limit switch must be built into the rotary mechanism, which in the
initial position stops the rotation in the horizontal direction. Such a
limit switch is originally built in vertically, but in the horizontal
direction - for reasons incomprehensible to me - it does not exist, so
we have to build it ourselves. It's not too difficult to solve, but it
requires a bit of creativity depending on who has what tools and limit
switches available. In all cases, make sure that the switch is active
in only one direction. One possible solution is shown in this figure. In this figure:
1 - vertical rod on the gear
2.3 - limit switches
4 - lever for switching limit switches
5 - gear
6 - auxiliary panel on which the lever shaft and limit switches are
mounted
The
advantage of this solution is that the limit switch is in both
directions and the required range of rotation can be set by correct
adjustment of the lever arms.
The antenna should be mounted on the rotor so that the overturning is
the same on both ends. In this case, the value of the overturning in
the counterclockwise direction is entered as the azimuth offset value
in the menu.
Limit switch connection:
Settings:
The most important parameters can be accessed
in the menu. You can get here by pressing the middle button (STOP) for
a long time. In this case, a multi-line menu appears in which you can
scroll to the appropriate menu item. These are the following:
AZ turn to:
here you can set where the antenna should turn horizontally when you
exit the menu
EL turn to:
here you can set where the antenna should turn vertically when you exit
the menu
Pulse/degree:
here you can set how many pulses the rotator gives for turning 1 degree
Azim offset:
how many degrees is the zero point of the antenna from the left end
position
Elev. offset:
how many degrees is the horizontal position from the limit switch
Max. azimuth:
the position of the antenna in the right end position
Max.
elevation: the maximum permitted elevation in the antenna
system's vertical beam (90 or 180 degrees)
GS232:
A or B, depending on which type you emulate
Beeper type:
if the value is OFF, the beeper is turned off, it does not sound if a
command is received on the serial port, DC - in case of an active
beeper, or a number that represents the frequency of the beeper. Its
value can be between 200 and 5000.
Elevation:
ON or OFF, if the rotator is not suitable for vertical rotation, set
this parameter to OFF
Overturn:
ON or OFF, if the antenna allows overturning, then by switching this
parameter to ON, the rotator can be used continuously between the value
set with the horizontal offset and max.
azimuth. In the OFF
state, only between 0 and 360.
Autoturn:
in the ON state, if the CW, CCW, UP or DOWN button is pressed for 5
seconds, then after the button is released, the antenna continues to
rotate until either one of the buttons is pressed again, or the rotator
reaches the end position.
Zero point:
this parameter determines where the mechanical zero point of the
rotator is, it can be south or north
WiFi:
how WiFi should behave at startup. You can turn it off or set it to try
to connect to the WiFi network at startup. If that doesn't work, switch
to AP mode.
Backlight:
the intensity of the background light
COM baudrate:
speed of the serial port
Menu char.:
font size of the menu - larger letters have better readability, but
fewer
lines, or smaller letters for more lines visible
Screensaver:
in case of 0, it is switched off (the display
lights up continuously), in case of a number, the display switches
off after this number of seconds
Display type:
display type, 1.9, 2.4, 2.8 col
Minimal turn:
The minimum rotation speed of the rotator at which the antenna still
rotates reliably.
When starting, it accelerates from this speed to the maximum speed,
before stopping it slows down to this speed so that the rotor is not
hit by strong impacts. Thanks to this, the movement is more continuous
even when tracking a satellite.
Background:
color combinations used on the display
Timezone:
set your own time zone if you don't want to see the time in UTC. (Time
difference between UTC and winter time. Daylight saving time is set
automatically)
Calibrate
to calibrate the rotator position. In the horizontal direction, it can
only be used with the subsequent installation of the limit switches, in
the vertical direction, the limit switch is already installed at the
factory
If the WiFi SSID and password are set correctly, you will see the
received IP address in the upper left corner of the menu window. We can
access the settings page in a browser using this IP address. The
firmware version is in the upper right corner. In case of a successful
connection, the UTC or local time, based on the timezone setting, is
displayed in the lower section of the screen.
Website with settings:
A file named rotor_s3.cfg can be found in
the
memory. It contains the set values of the parameters. It's a text
file, but I recommend editing it by hand only if you know what you're
doing. Manual editing can be beneficial when entering the SSID and
password for the first time, if we do not want to connect via the AP
number 192.168.4.1. However, setting the SSID and
password can be done in a much more secure way via the serial port with
the { and } commands. If the controller cannot connect to the WiFi
network, and if this function is not disabled, it creates an AP that
can be reached either with the ROTOR-AP SSID or with the IP address
192.168.4.1. In this case, the password is 1234567890. If you want to
use WiFi, make sure to check in the menu whether WiFi is ON. If not,
turn it on. In this case, automatic connection is in effect (the
controller must be restarted, because it only checks the settings when
it is switched on). We can
change this setting via the website.
The third way to set the parameters is to send the
appropriate commands on the serial port. The list of commands can be
retrieved with the command H or h.
Assembly:
As you can see the PCB is quite simple. It
contains only some parts and
the connectors. There should be no major problem with the
acquisition of the parts either, because the value of each resistor is
10 k, and the ceramic capacitors are 100 nF. Their size is 0805. Except
for the
zener and protection diodes, all diodes are shottky.
The display and push buttons have been placed on a
separate panel.
Each display size has its own panel. The 1.9-inch display panel
has
5.8x5.8 mm buttons, while the 2.4 and 2.8-inch displays have 8.5x8.5
mm buttons.
The following gerber files can be used for the production of PCB
panels:
logic, 1.9display, 2.4display,
2.8display
Since the WiFi antenna is located on the module, make
sure the
controller is either installed in a plastic box, or the metal box is
not too closed so that the WiFi signal gets out of the box. Due to
cooling needs, the box should not be too closed anyway.
Box made with a 3D printer for the controller with
1.9 , 2.4 , 2.8 inch display.
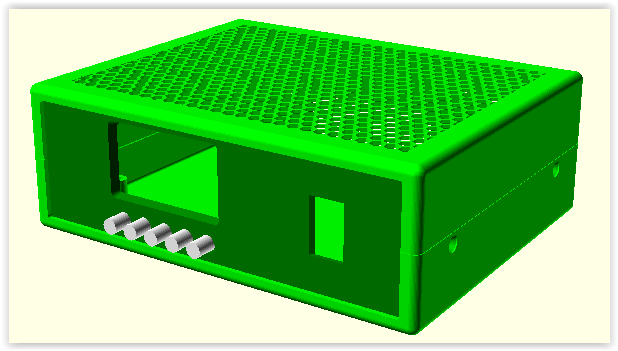
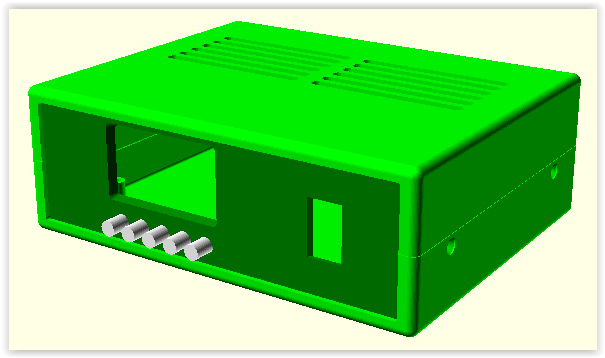
lid_xxh
lid_xxv
The power supply is not part of the controller. As a power supply
unit, choose a type that can withstand sudden changes in current
consumption. I use a 24V 10A power supply used for LEDs. I adjusted its
voltage below 20V with the help of the trimmer included (to the minimum
that can be set). The
value of the D6 diode is critical. A Zener diode must be used that,
when turned off, the ESP32 - 21 port (interrupt) goes to the LOG0 state
in time so that the processor has enough time to save the current
position, but the voltage fluctuation that occurs when starting the
motors (the current can be as high as 10A) does not activate the
interrupt. This largely depends on the quality of the power supply.
Installation:
If you already have experience using micropython and
the ESP
module, you should fill the content of the program package into the
module in the way you are used to.
If you have no experience or are using the ESP32
module for the first time, follow the
instructions below.
1. download program Thonny
to the operating system (I recommend using Windows).
2. create an arbitrary directory where you copy the following file firmware
Extract the contents of the firmware package to a new directory, e.g. ROTOR.
Connect the ESP module to the computer with a USB
cable. In the Windows system, check the port number assigned to the ESP
in the "Device Manager" menu. If the system does not recognize
the module, install the following driver CH343SER.
First option:
Windows:
open the install_upython.bat file
correct the port number (python3 must be installed)
save the file
run the bat file
Linux:
run the sh file: bash install_upython.sh
Second option:
Download the programot to load uPython and the uPython
When we start the loading program, a window
like this appears:
Here, select ESP-S3 in the first row:
Pressing OK brings up the program itself:
Use the ... button to load the bin file, set
the COM port number to the one
the ESP received. The first step is to erase the contents of the ESP
memory with the ERASE button. When it's done with that (it will take
a while), load uPython into ESP by pressing the START button. If this
operation was also successful, we are already over the most difficult
parts.
Now we can start Thonny. In the Tools - Options
menu, set the following:
Of course, in the second option, the port number of our own module must
be entered.
In the View menu, select Files. After that a
simplified file manager
appears on the left side. In the upper half, enter the directory
where the firmware can be found. The files in the upper window should
be
copied one by one to the lower window (right click - Upload to /). Make
sure that the fonts in the fonts directory needs to be included in the
fonts directory on ESP too. With the right-click Upload to /, the
entire font library can be copied at once.
This operation completes the installation of the
firmware. Unfortunately, it has happened to me that the content of the
file was corrupted during copying. If the icon shown in the picture is
not displayed next to the name of the file, the copying must be
repeated. You will not have the "rotor.dat" file yet. It is created
only after the controller is turned on.
partlist
A version for a 4-inch touchscreen display has also been prepared:
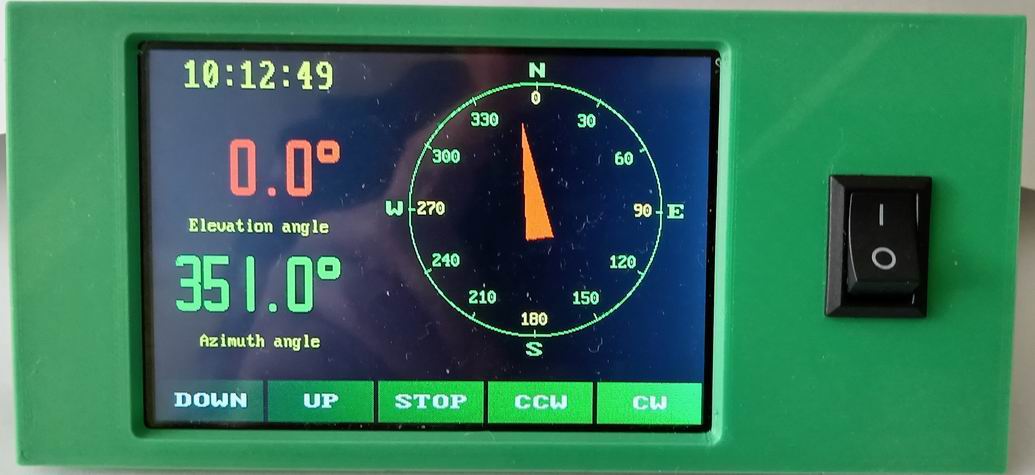
The above instructions are also valid for this version. The difference
is that the touch sensor driver must also be installed (ft6x36.py). The
firmware is not compatible with the old one, so the files in
firmware_96.zip must be installed in the ESP32. The method of
connecting the control panel and the display can be found in
connector.txt. Since there are no buttons, a separate panel is not
required for the display, it is enough to connect the pins of the
connectors properly, or create an intermediate board based on the image
below. For quick adjustment, a potentiometer(s) can also be used in
this version. If there is elevation control, then by touching the
center of the azimuth circle, the potentiometer position will be
displayed instead of the azimuth and elevation. The current position of
the azimuth potentiometer is also shown by the point outside the
azimuth circle. By touching the azimuth field, the antenna turns to the
position specified by the azimuth potentiometer. If the elevation field
is touched, the elevation turns to the direction specified by the
potentiometer. If the rotator is used for horizontal rotation only, the
current position of the potentiometer is permanently visible in the
elevation field. In this case, this field must be touched to rotate the
antenna in the desired direction.
If we do not use a potentiometer, the point
outside the azimuth circle shows the position given by the external
command (where the antenna should turn).
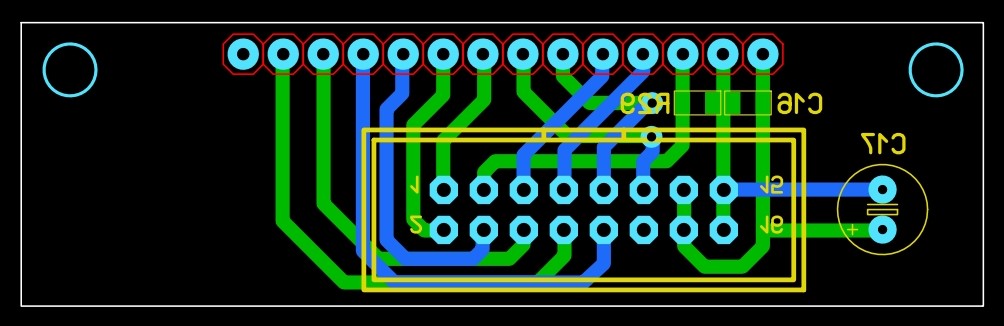
If you prefer push buttons (or have a display without a touch sensor),
or if radio frequency interferes with the touch display (unfortunately,
capacitive sensors are prone to this), you can also use it with push
buttons. For this type, you can use this PCB:
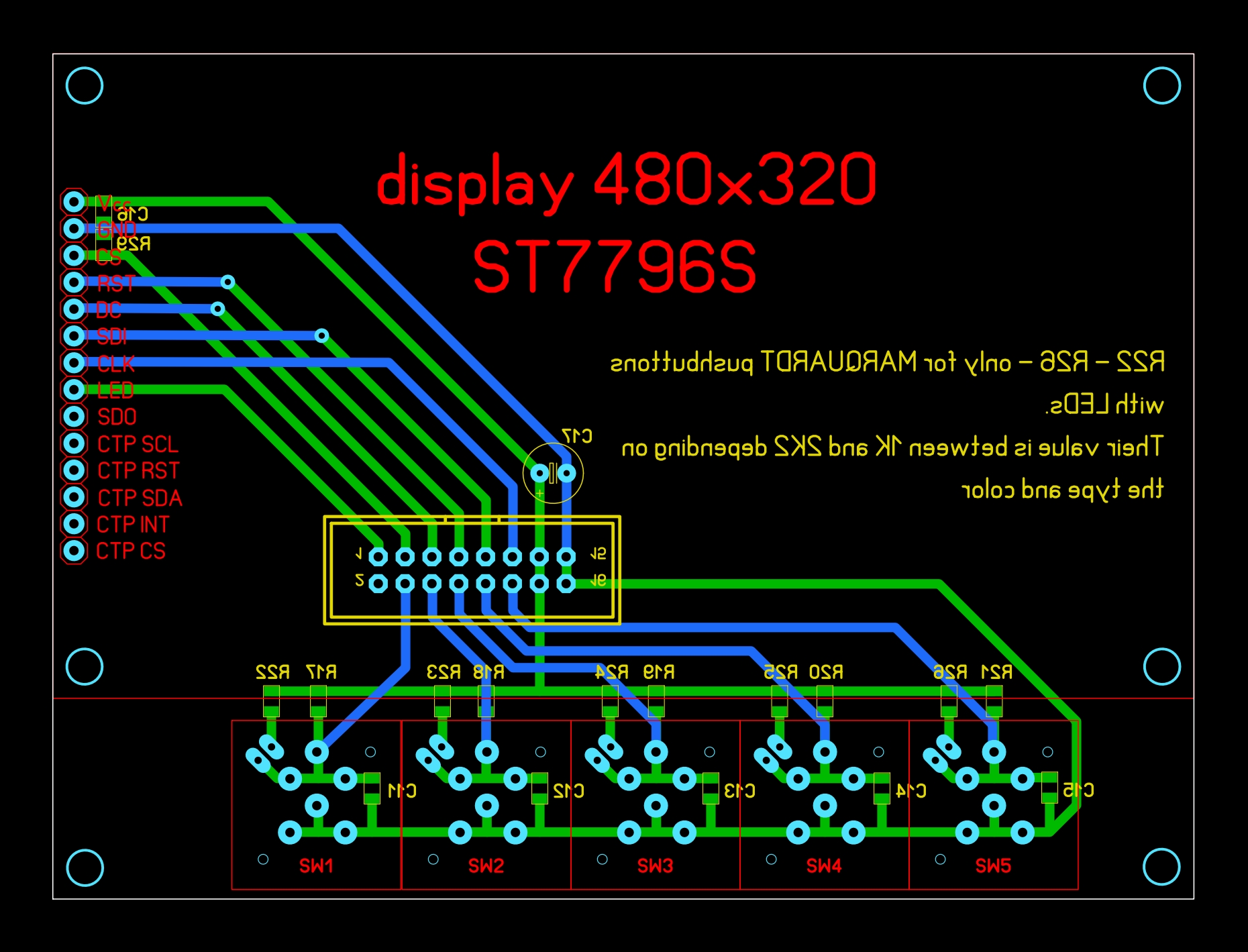
Here are MARQUARDT type push buttons are used. These are much more
pleasant to operate, they react gently and reliably. We can also use
buttons with or without LED.
gerber file for making the PCB: display40
Universal
firmware this can be used for push button and touch sensor displays.
Options for purchasing parts:
ESP32
module
Motorcontroller
UART-COM
level converter
1.9"
display
2.4"
display
2.8"
display
4.0" display
stabilizer
switches
beeper
single
row female conector
ribbon
cable connector
socket
header connector
main
switch 15x21
power
supply or here
green
connectors or here
or
PV05-5.08-H-P EUROCLAMP
PV02-5.08-H-P EUROCLAMP
PV02-5.08-V-P EUROCLAMP
SH05-5.08 EUROCLAMP
SH02-5.08 EUROCLAMP
MARQUARDT Square Key Cap Round
A satellite tracking program was also created to control the antenna,
which can be found at this
address. With this program, it is possible to automatically track
several satellites.
The drawings and the program in the processor are the intellectual
property of the author. Its commercial use is only permitted with the
written consent of the author!